Atlas-SSI Curbs Plastics Pollution, Protects Aquatic Life, and Improves Worker Safety
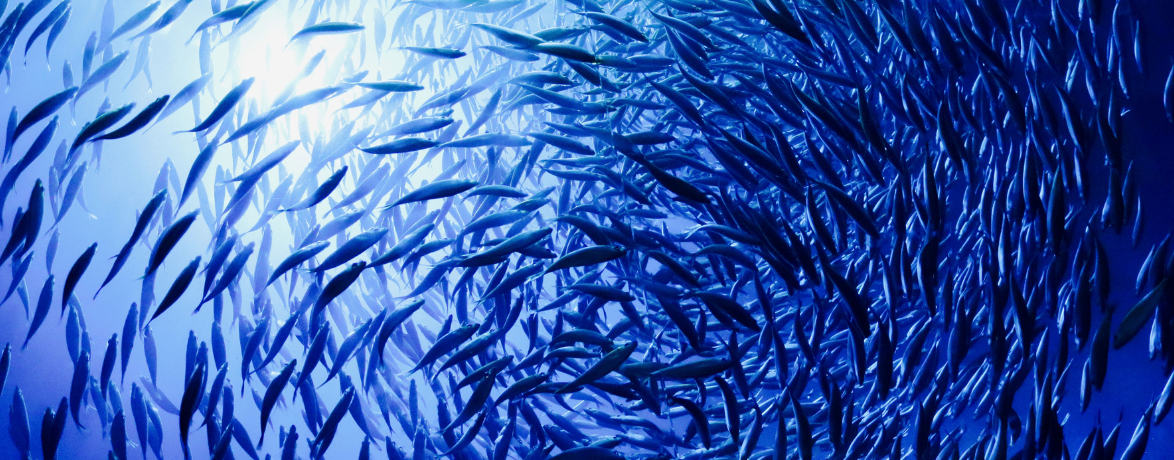
Water is a critical resource for economic growth. Across the United States, thousands of industrial facilities, including power generating stations and product manufacturers, use large volumes of water from rivers, lakes, and oceans to cool their plants; they depend on water to keep their operations running smoothly.
The traditional design for cooling intake systems protects the infrastructure and plant operations. Paul Lewis, CEO of Atlas-SSI, says that today, these end users have considerably bigger concerns about how their water use impacts the broader surrounding ecosystem.
As North America’s largest full-service traveling water screen and bulk material handling equipment manufacturer, Atlas-SSI has offered industrial customers their “first line of defense” of their critical assets for more than 50 years – robust screens that prevent debris from entering their cooling intake systems. In recent years, however, global challenges such as pollution and climate change have shifted the scope of their customers’ needs and, accordingly, the demand for innovative solutions.
“When our customers design and upgrade their systems, they must consider how to meet new regulations, make operations more efficient, and minimize their environmental impact,” says Lewis.
Atlas-SSI has set out to lead the way in the industry, he adds. “Our team is addressing global water challenges, meeting emerging customer needs, incorporating innovative technologies and services, and growing to serve new markets.”
Protecting aquatic life
As part of the global effort to build climate resilience, many regions are publishing new regulations that recognize the value of biodiversity and protect ecosystems. Cooling water intake structures can pose threats to aquatic life, and, as one example of these rules, Section 316(b) of the Clean Water Act governs the design and operation of these structures to protect these species.
Atlas-SSI’s customers are looking to comply with Section 316(b) with cost-effective solutions. “We are uniquely equipped to help,” Lewis says. “With our technology, we can capture and safely return aquatic life to the waterways. As a result, our customers are now helping to stabilize and grow these populations.”
>>LEARN MORE Atlas-SSI Case Study: East River Generating Station
Preventing plastics pollution
Global awareness of the threat of plastics and marine debris to human and ecosystem health is growing, in part due to widespread reporting on phenomena such as The Great Pacific Garbage Patch. In many regions, regulators have responded to this concern with new standards that target sources of pollution and aim to improve the quality of the water that end users return to oceans, lakes, and rivers.
“Removing plastics and debris from water has never been more important,” Lewis says. “For many of our stormwater customers, our systems are the first line of defense. By removing plastics, we’re preventing large amounts from entering waterways and beginning to decay and generate additional microplastic pollution, affecting aquatic life and, eventually, humans.”
He adds that Atlas-SSI’s screening equipment is helping eliminate immediate pollution by capturing millions of pounds of plastic per year. “As more installations come online, that number is growing – we’re looking forward to helping our customers divert and redirect this waste.”
Circular manufacturing and improving worker safety
For more than 30 years, Atlas-SSI has taken a circular approach to traditional equipment servicing, including offering rehabilitation services for its screens. “We work with our customers to rebuild equipment rather than replacing it outright,” Lewis says. “We believe strongly in safely reusing materials and extending the life of our infrastructure. For example, a typical water intake screen weighs about 10 tons, and it takes 1.85 tons of carbon to make one ton of new steel. By reusing steel components, we’ve saved more than 4,200 tons of C02 emissions to date.”
Today, the company is also taking steps to further improve worker safety, since inspecting, maintaining, and rebuilding underwater screens requires specialized diving service crews. To do their job, these crews must often contend with fast-moving water or murky conditions, and they don’t always know what they’re going to find.
Lewis and the Atlas-SSI team are beta testing new technology that allows teams to safely investigate equipment using robotics, ROVs, with cameras and sonar. “With information gathered by submersible ROVs, for example, we can better prepare our crews for the work they need to do.”
Robotics can also make the team’s work more efficient, Lewis adds. “It takes about an hour to get a diver in the water,” he says. “They have a pre-dive checklist that involves calibrating breathing tools, transporting heavy equipment, and testing radio communications. With an ROV, we can just pop it in the water and get a quick look to better plan our dives.”
Growth in new markets
As regulators require end users to meet new and more stringent standards for water quality and ecosystem health, Atlas-SSI is seeing new opportunities for growth. For example, the company recently won a contract to install its 316(b) compliant traveling water screens at a large desalination plant.
Lewis and his team are also seeing opportunities for Atlas-SSI to participate in the transition to clean energy, and recently acquired a company called Cooling Tower Valves and Screens, LLC to offer greater efficiencies to this market.
“When we started our company, the primary market was power. Today, more than half of our revenue comes from other markets, and, with recent acquisitions in the municipal sectors and supporting the alternative energy sector, we’re continuing to build integrated solutions and grow and diversify our business,” Lewis says.